Build Blog 6: Mechanical Progress
- Kyle Tam
- Mar 3, 2023
- 3 min read
Hi everyone! This week's blog post is focused on our mechanical progress, and the related integration work.
Mechanical
Overview
Last term we finalized the structural design of the system and began ordering materials to begin manufacturing. In the last few weeks, we've begun manufacturing of the structure, electronics, and fluidics systems and finalized the design of the plant trays. I'd like to take a step back and give a quick overview of some of the major components of the system and then discuss our progress further.
The mechanical design of the system is composed of a robust structure made from AISI 1018 structural steel tubes that can be easily assembled under an hour. This strong structure supports a number of key components including two removable stainless steel plant trays that can accommodate up to 45 heads of lettuce of 3 tomato plants. Grow lights are found above each tray to provide additional lighting while water lines can be found routed along the sides of the structure to provide water to the reservoir to the trays and back again. The reservoir, water pump, electronics package, and nutrients and pH chemicals dispensing unit can all be found at the bottom of the tray where they will not need to be accessed by the user frequently.
Structure
The design of the structure was finalized last term and manufacturing has been ongoing this term. The parts of the structure were relatively easy to make, with a total of 4 unique tubes and 2 types of brackets to manufacture. These tubes had to be cut down to size, drilled, tapped, and then cleaned and painted before they could be assembled. The brackets were cut using a waterjet cutter and then sanded down before painting them. Due to the sheer amount of holes on the tubes, the manufacturing took a while, but in the end this led to very easy assembly as similar parts could be interchanged.
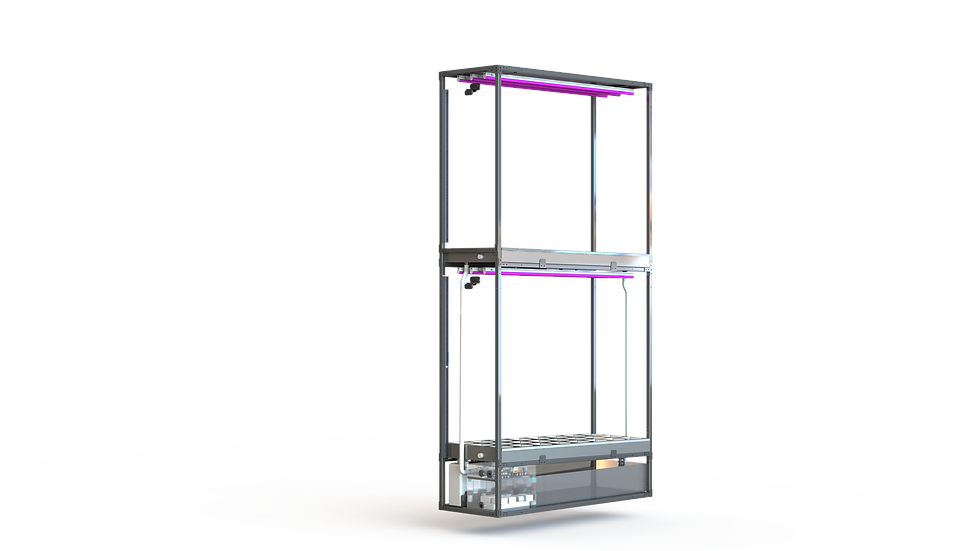
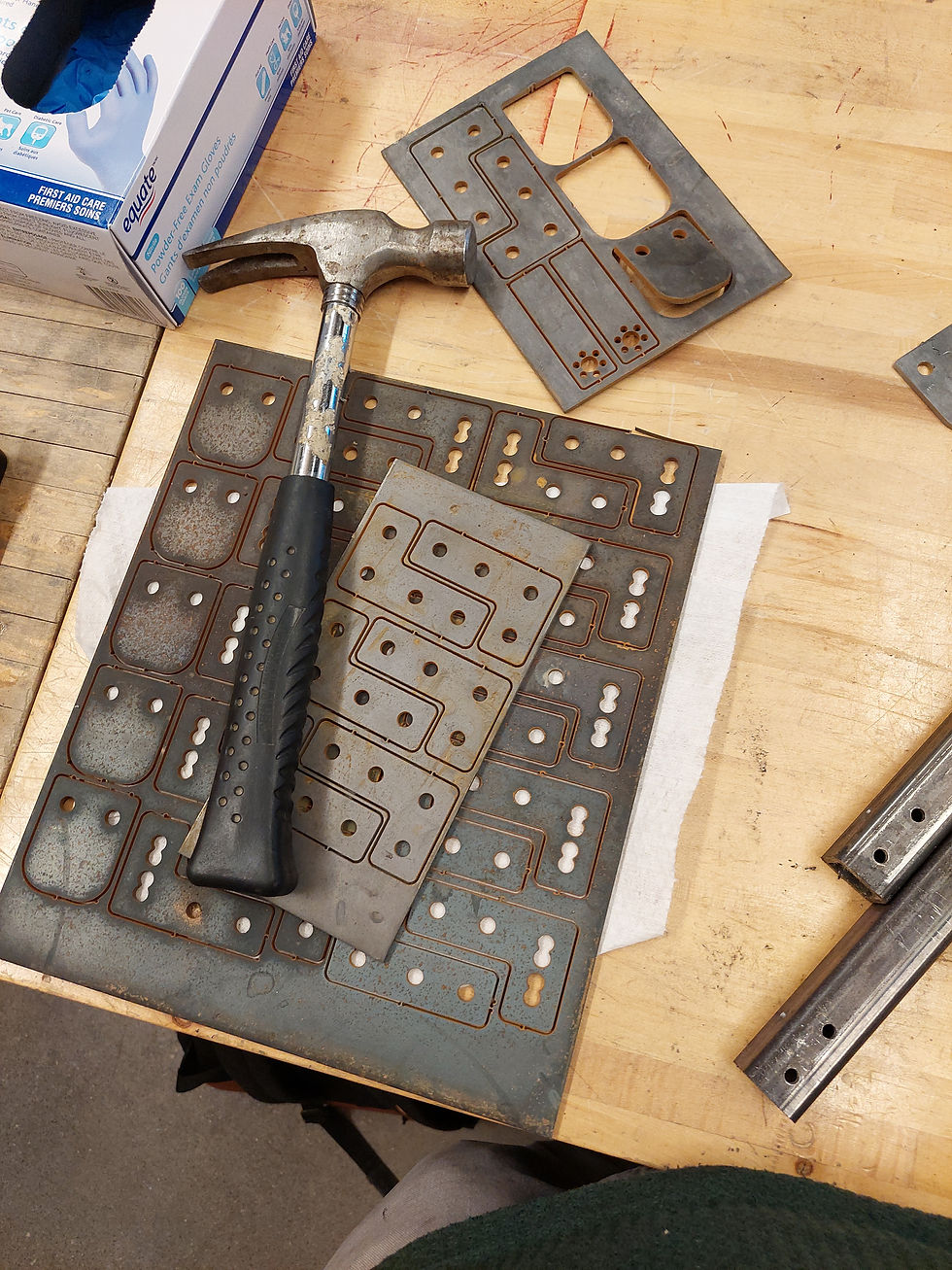
Additional components such as the light supports and tray guards were manufactured afterwards. These components were relatively easy to manufacture using 1/8" sheet metal and steel angle.
Electronics Package
While the structure was manufactured, the electronics enclosure was being fabricated in parallel to facilitate integration with the electrical hardware. Since the electronics were composed entirely of commercial-off-the-shelf (COTS) hardware, the system did not require further CSA safety certification, thus the enclosure was designed for ease of access and display. This resulted in an enclosure laser-cut from acrylic with electronics mounted to a custom 3D-printed base board. The low-power electronics were placed above the high-power equipment to isolate any electromagnetic interference and to facilitate any troubleshooting that might occur at a later time. In the end, this resulted in an elegant and easy-to-use package.
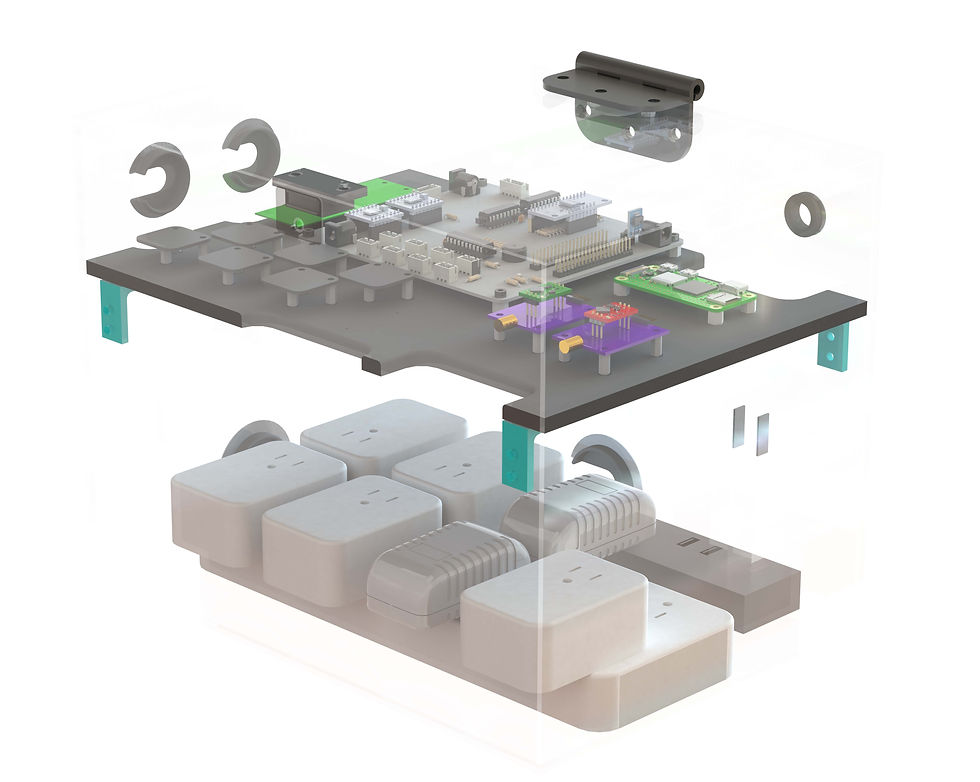
Fluidics and Dispensing System
A lot of progress has been made these past few weeks refining the design of the fluidics system to make it more manufacturable. This system is composed of two water trays bent from 24 gauge stainless steel sheet metal and secured with two rigid end plates using industry standard adhesive. Additional plant trays are manufactured from sheet metal with square cutouts where custom 3D-printed holders will be able to support a fully-grown lettuce or tomato plant.
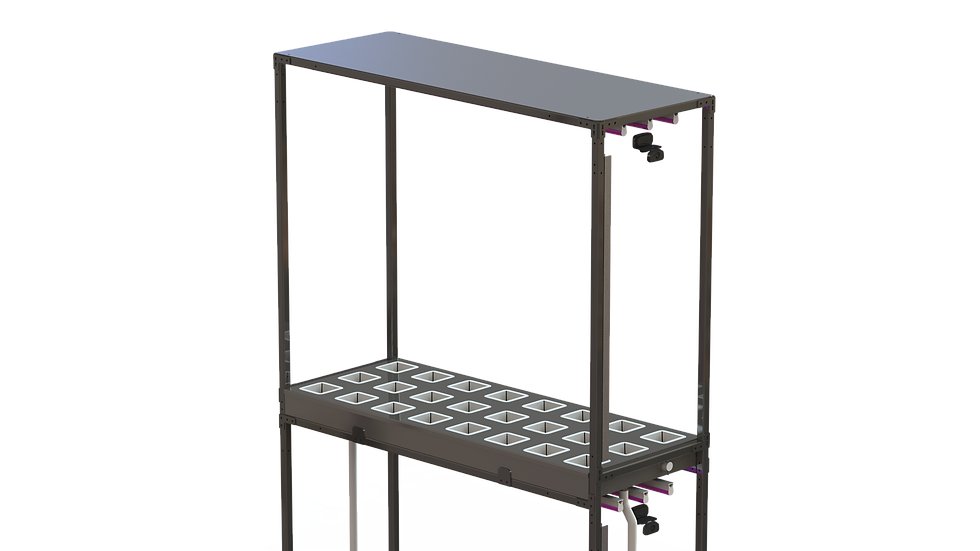
Recent progress has refined the design to make these features more manufacturable. The plant trays were recently broken into smaller sections so that they could be manufactured via water jet and secured together using stainless steel rivets. The water trays were recently manufactured and after carefully gluing them and sealing them, they withstood a long term leak check on the first try!
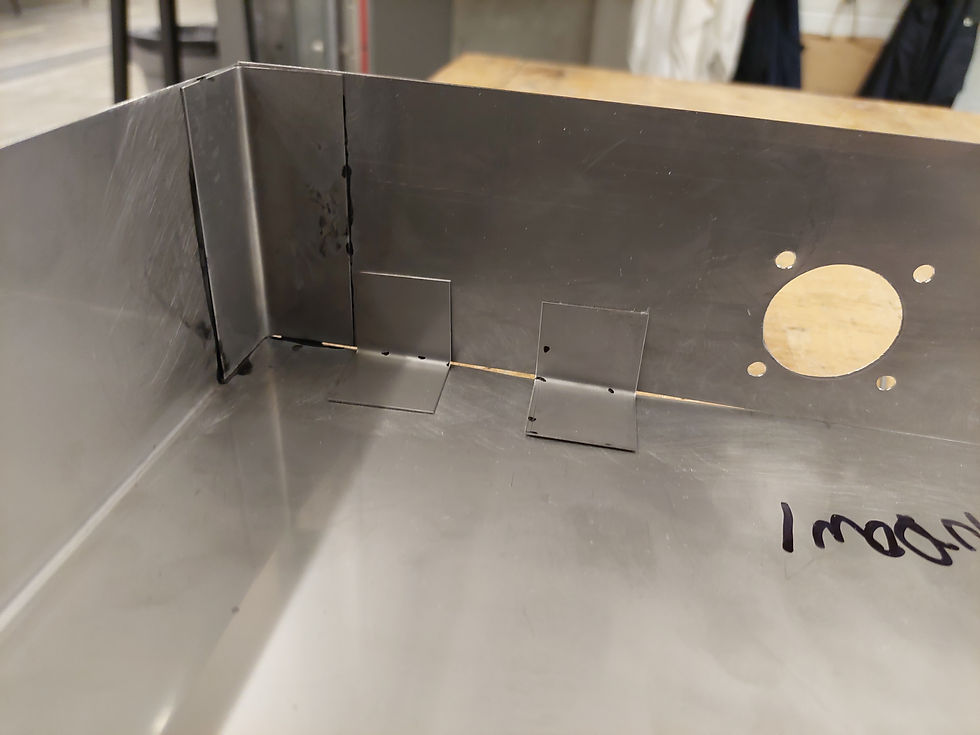

Assembly and Integration
After manufacturing all of the core components of the system, it was time to put everything together and see how well it fit!
First thing to be assembled was the structure. Overall, the structure wasn't too difficult to assemble. Due to the symmetry of the structure, the two halves of the structure was assembled on the ground before they were raised up together and attached. The only issues that were encountered were a very misaligned holes with the brackets. A byproduct of manufacturing by drill press - need to get good for a production model!
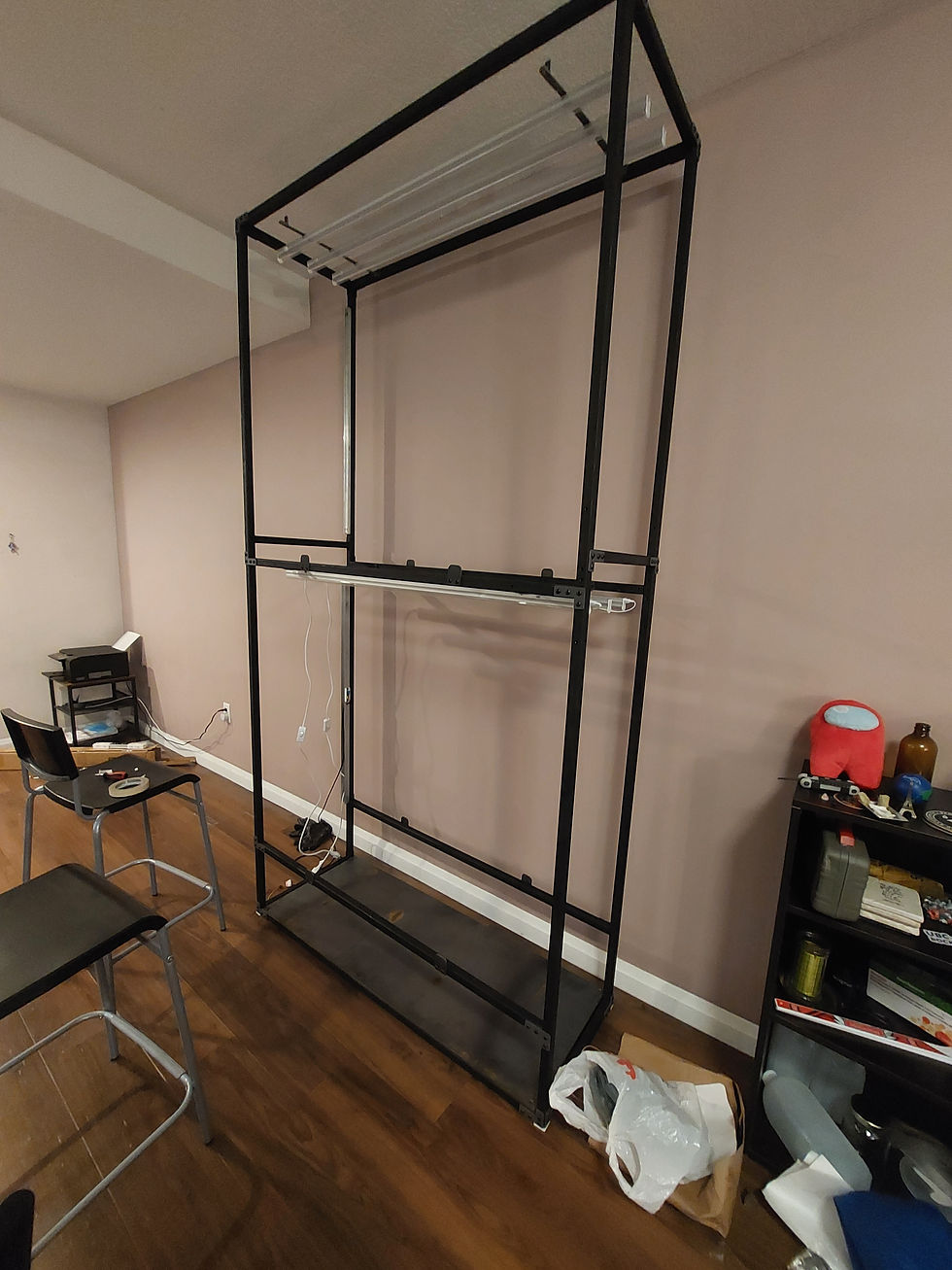
In parallel, the electronics package was assembled after a number of test prints to verify all the electronics, sensors, and wiring would fit together. Overall, not too shabby.


Lastly, the remaining the fluidics system was integrated into the structure and electronics. This included adding the leak-proof water trays, the reservoir, nutrient dispenser, and plumbing so the real magic could begin!
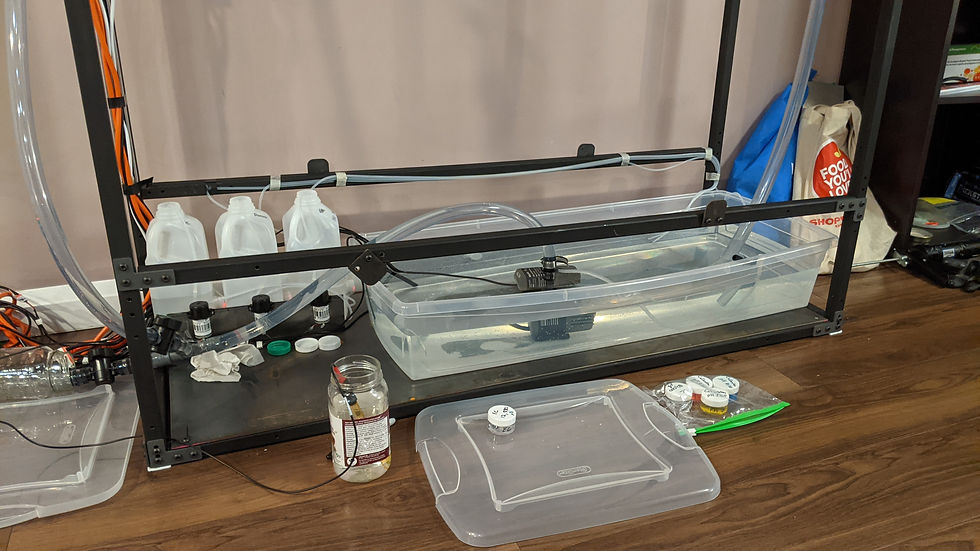

What's Next?
With all the core elements manufactured, assembled, and integrated into the system, only a few parts are left to be made. These include the plant trays (see below for a sneak preview of the first trays manufactured), the cover panels, flow restrictions, and the sliding mechanism for the nutrient dispensing module.
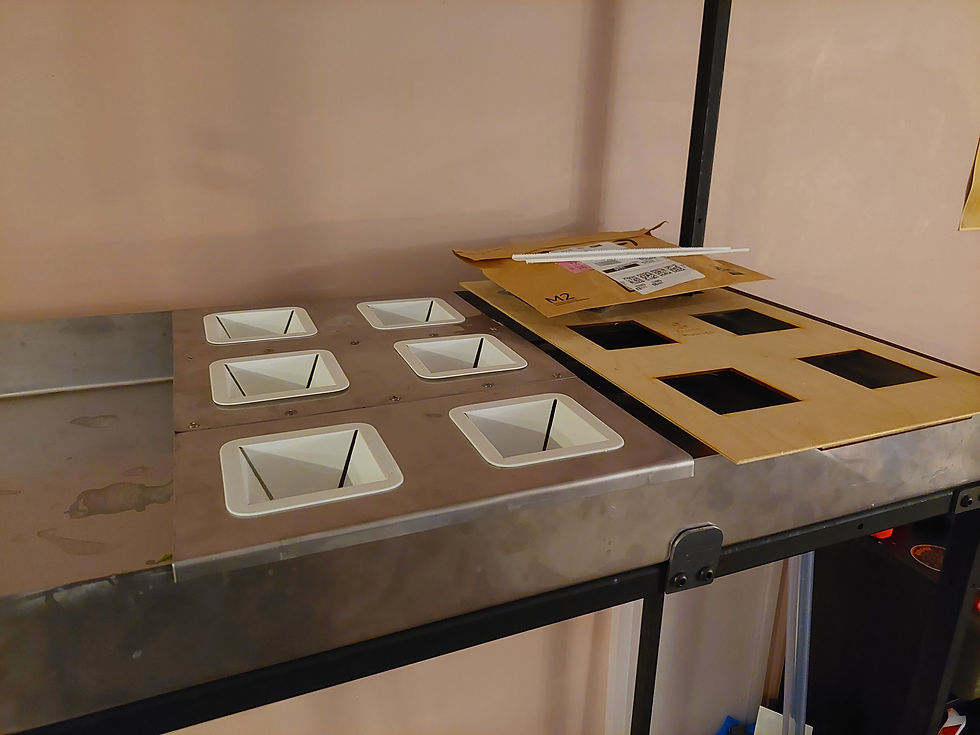
Stay tuned for more exciting progress as we near the end of our final demo! Thanks for reading!

Comments